Responsible culture:
Health, safety and wellbeing
We strive to ensure everyone can go home safe and well every day
Our safety approach focuses on people. Enabling employees to stay safe and healthy at work is a prerequisite for any responsible company. By empowering our people to adopt safe behaviors at work, we can also have a wider positive impact when they take the same safe behaviors home to their families – so we promote a 24-hour safety and health mindset.
As a global employer operating in more than 60 countries, we have an impact on the health and safety of our 9,000+ employees. Impacts on people and their human rights can occur if health and safety is not assured as people can sustain heavy injuries or suffer chronic diseases. Our focus on preventing injuries and promoting health and wellbeing avoids such impacts and also supports our business by reducing lost time, enhancing productivity and improving employee engagement.
Our main safety risks
1 Working at moving and rotating equipment
2 Slips, trips and falls
3 Operating forklift trucks and other vehicles
4 Handling cutters and knives
We address these risks through ongoing investment in business-wide improvements
such as additional safety devices on machinery.
Our Life Saving Rules
1 Work with a valid work permit when required
2 Check equipment is isolated before work begins
3 Obtain a permit for entry into a confined space
4 Use fall protection when working at height
5 Wear a seatbelt in motor vehicles when provided
Golden Rule
Intervene to stop work if conditions or behaviors are unsafe.
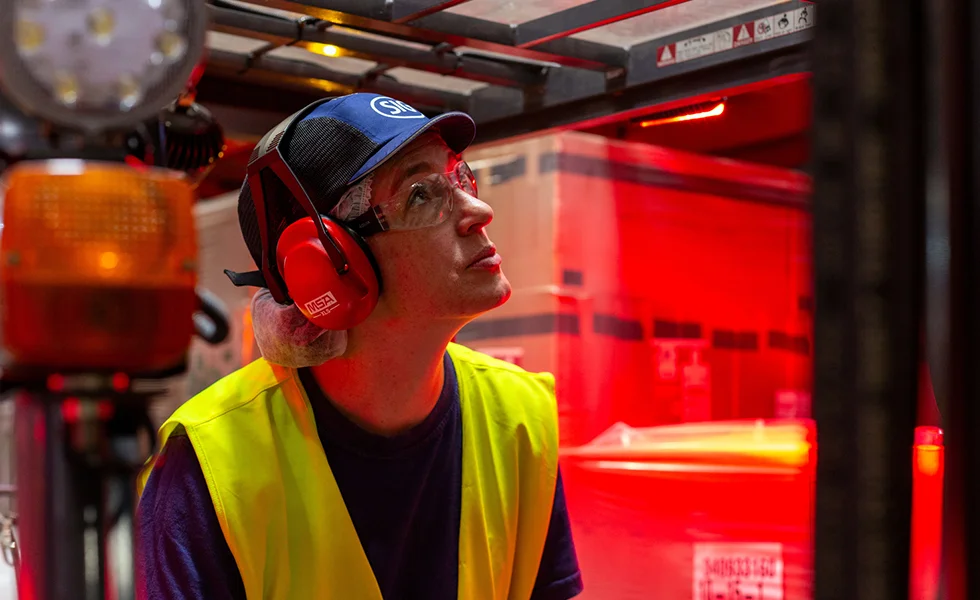
Our commitments
We are committed to adopting a preventive health and safety strategy through our “Take Care” culture for workplace safety and strive to prevent all health and safety incidents and work-related illnesses. We also commit to regularly conduct workplace and task-based risk assessments as part of our proactive approach to the workplace safety protocol and our “Take Care” culture.
We strive to:
- prevent work-related incidents and illnesses
- manage risks
- empower employees to adopt safe behaviors
- support health and wellbeing
Our approach
Health and safety
Keeping the conversation going on safety
Safety is one of SIG’s core values and it is fundamental to everything we do. Most of our biggest risks are at our production plants. 100% of workers at our production sites, as well as our Global Assembly, Global Technology and Technical Service functions, are covered by an occupational health and safety management system.
We address risks through safety awareness campaigns focusing on specific topics, with a simple overview and a clear structure explaining why it is important, what risks are involved, and what actions are planned to mitigate the risks. Plant managers, team leaders and shift managers are present to stimulate discussions during team meetings. The most important messages are collected and in turn shared.
Managing risks
The safety and health of all our employees and contractors is covered by our robust health and safety management systems which promote continuous improvement. These systems are certified to ISO 45001 standards at all production plants in the SIG Group. All employees and contractors working on our sites, as well as visitors, are required to adhere to policies and procedures as set out by the management systems. Customers are instructed on health and safety risks at our training centers.
We conduct annual risk assessments at each site and are committed to monitoring incidents and near misses, systematically analyzing their root causes and targeting improvements through local corrective action plans. We also recognize sites that have achieved exceptionally strong safety performance through our SES Maturity Assessment and Safety Awards scheme.
Our risk assessments and corresponding operating instructions form the basis of our approach to chemical safety in the workplace. Risk management is legally required in every country where SIG produces and each location needs to fill out a form on Environment, Health and Safety (EHS) compliance with national law.
Empowering employees
Everyone at SIG is trained in health and safety, including our Life Saving Rules which target the biggest risks to our people. Training for each employee covers how to manage risks specific to their role – in our production plants or offices, working from home, or providing technical service support at our customers’ sites.
We empower our people to provide input and constructive feedback on safety and risk. All aseptic carton plants where our observation safety program is established must ensure that at least 15% of employees have completed training. The bag-in-box and spouted pouch plants started to train and develop simple observation safety programs in 2024. We track progress as part of our monthly health and safety metrics.
Our health and safety steering committees in the plants include plant management and employee representatives, as well as other participants such as local EHS managers, People & Culture teams, works council representatives and medical doctors. Local workers’ councils or committees meet regularly to discuss health and safety matters.
Managing health and safety
We maintained global certification to the ISO 45001 standard for health and safety management across our aseptic carton production plants and extended it to all our production plants in 2024, including bag-in-box and spouted pouch.
The SES (SIG Excellence System) is a SIG-specific assessment and represents a temple made up of foundations and pillars showing the interaction of specific tasks. The aim of the SES is to analyze our systems and to approach improvements methodically.
Results from the EHS pillar flow into the overall score of the SES Maturity Assessment. The SES process takes place once a year in all SIG plants and forms the basis for the global exchange of best practices and further opportunities for improvement.
For all SIG plants regular audits following SEDEX SMETA – which include health and safety – are conducted every two years. Three additional plants which went into operation since 2023 were audited in 2024 while the remaining plants were last audited in 2023 and are scheduled for their next audit cycle in 2025.
Responsibility for managing health, safety and wellbeing
- Global EHS reviews health and safety performance with the local management and local EHS leads; monitors and manages the sustainable implementation of safety projects and EHS alerts; and provides regular reports to the Group Executive Board.
- Head of Operations is responsible at operational level.
- Group Human Resources is responsible for employee wellbeing.
- Regional leaders are responsible for EHS across our businesses in each region and are part of a broader network to learn from each other.
Assessing effectiveness
Health and safety KPIs are reviewed by the GEB each month. The GEB also receives quarterly reports on health and safety matters. The Board is regularly updated. We have annual site self-assessments (based on ISO 45001) and internal audits/assessments and perform SEDEX SMETA site audits and EcoVadis assessments. We monitor incidents and near misses. Issues or concerns can be reported via the Integrity & Compliance Hotline and via safety opportunity cards and the behavior-based safety process.
Measures taken in 2024
- We ran a global campaign to raise awareness of safe work behavior with the aim of eliminating safety incidents relating to moving and rotating equipment. The campaign started with the sharing of real experiences and stories to which colleagues could relate. This was followed by task identification to understand which activities in our plants are potentially dangerous, and hazard hunts to identify equipment risks.
- In August, we started integrating our new greenfield operation in Ahmedabad (India) into our established health and safety management systems. Based on the Life Saving Rules and a comprehensive induction phase, we are sensitizing all new employees to keep them safe and healthy at work and consider the safety risks associated with our business. We run regular meetings and trainings for plant leadership teams to guide them on how leaders can help to strengthen the health and safety culture.
- Our new plant in Querétaro, Mexico completed its first ISO 14001 and ISO 45001 certification audits with no non-conformities.
Total recordable cases1
Total recordable case rate1
Lost-time cases1
Lost-time case rate1
Reporting on safety incidents in 2024
- 14 of our sites have not experienced any accidents in 2024
- 6 sites had no lost-time case
- We maintained our record of zero fatalities across SIG Group
For detail on recordable and lost-time cases, see KPI table.
Injuries by type in 2024
(%)
Injuries by cause in 2024
(%)
Supporting health and wellbeing
We are committed to supporting the health and wellbeing of our employees. We take a holistic approach that encompasses physical, mental, financial, and social wellbeing to enable our employees to lead fuller, more productive lives both at work and at home.
Many of our larger sites offer access to medical professionals, health insurance, health check-ups and fitness programs. We continue to extend our behavior-based model to occupational health issues such as ergonomics, and we provide ergonomic workstations and training. Employees can access information on current offers and opening times at any time via the SIGer app, as well as through posters, banners, and other on-site communications. We also recognize that musculoskeletal health issues, such as back problems, can be an indicator of wider health and wellbeing issues. Our health rate among full-time employees was 97.8%1 in 2024 – up from 97.7% in 2023.
Reducing stress and promoting work-life balance
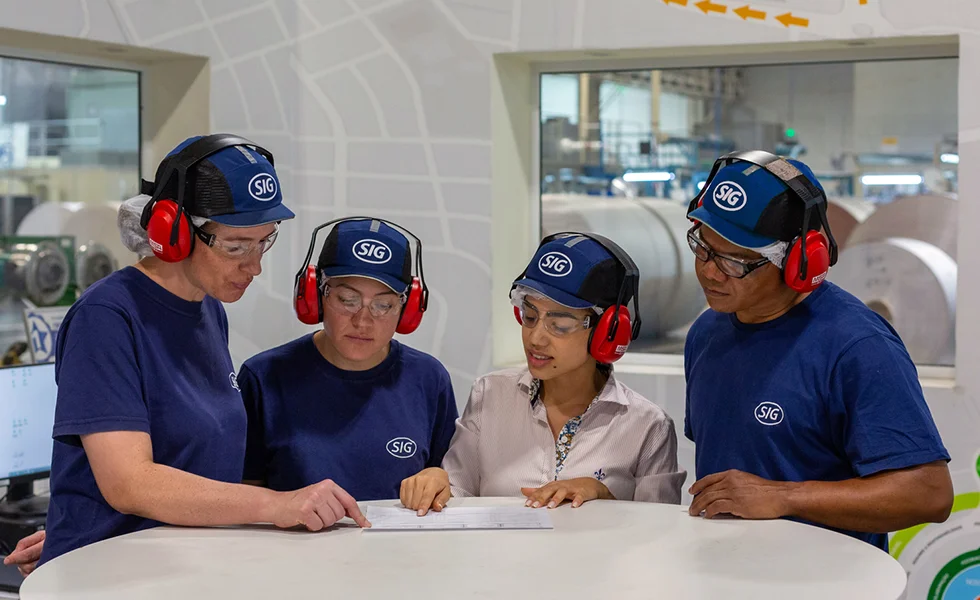
Measures taken in 2024
- We collectively celebrated and raised awareness on both global and local levels through various international celebration days, reinforcing our holistic approach to physical, mental, financial, and social wellbeing. These efforts have been highlighted through our Monthly Wellbeing Wednesday initiatives and have included a wide range of discussions and activities, such as:
- Sleep and productivity
- Psychological safety
- Stress management
- International Yoga Day
- International Day of Friendship
- The importance of having a wellness spot
- The importance of having regular medical check-ups
- We implemented our guidelines on ways of working for office workers and developed new guidelines on ways of working for employees working in production roles and in the field as service engineers. These set out clear guidance and tangible steps to support wellbeing and work-life balance.
- We have launched a wellbeing guide for managers to better identify and recognize colleagues who are experiencing mental health problems and want guidance on how to support them.
- We piloted an eTraining program specifically designed for leaders to help them foster psychological safety in the workplace, ensuring that their teams feel confident in bringing their whole selves to work. This initiative will be rolled out across the leadership levels of the organization in 2025.
- Emotional assistance programs are workplace-based services designed to support employees with personal or professional issues that may impact their wellbeing and job performance.
Leadership and wellbeing
In 2024, SIG emphasized the importance of leadership and wellbeing through a series of insightful podcasts featuring various leaders across the organization. These podcasts have served as a platform for open conversations about leadership and wellbeing.
13 senior leaders shared their personal experiences and approaches to leadership, resilience, and wellbeing. The podcasts gained significant attention on the SIGer app, fostering a culture of open dialogue and community support. Viewership metrics have indicated an engaged audience who value the insights shared, with strong participation from different regions.
Recurring themes from the series included:
- The importance of mental health and how it ties into strong leadership.
- Personal strategies for maintaining work-life balance, resilience, and self-care.
- The value of diversity and adaptability in leading teams through change.
- Encouraging a supportive workplace culture, where wellbeing is prioritized alongside performance.
These conversations have not only spotlighted the health and wellbeing journeys of senior leaders but also created a ripple effect across the Company, inspiring employees to prioritize their own wellbeing and contributing to a balanced, thriving work environment.
Our targets and performance
Targets, progress and performance
2025 target |
|
Progress tracker |
|
2024 performance |
||||||
---|---|---|---|---|---|---|---|---|---|---|
Health, safety and wellbeing |
||||||||||
Material topic: Health, safety and wellbeing1 |
||||||||||
Zero recordable cases2 |
|
|
There were 52 total recordable cases across SIG Group in 2024, 20% less than in 2023, result in a total recordable case rate for SIG Group of 0.63 recordable cases per 200,000 hours worked. |
|||||||
Define a holistic strategy and roadmap to foster wellbeing at SIG |
|
|
We rolled out our holistic program to promote physical, mental, financial, and social wellbeing through global awareness activities, guides, training, and a new podcast to equip employees and managers with know-how to support wellbeing. |
|||||||
|
Progress in 2024
- Reporting of near misses supports our efforts to prevent incidents. In 2024 774 near misses were reported (2023: 619) with a frequency rate of 9.46 per 200,000 working hours (2023: 7.7).
- The rate of severity2 of lost-time cases in SIG production sites was 1.26 (compared with 0.51 in 2023).
- There were also 12 lost-time cases among contractors working at our production sites this year and the lost-time injury frequency rate for contractors was 0.77 per 200,000 hours worked.
- 90% of employees participating in our global engagement survey agreed SIG does a good job of ensuring workers’ health and safety wherever we operate, 7 points above the 2023 industry benchmark.3
- We continued to encourage employees to observe and provide constructive feedback to correct unsafe behaviors.
- 19% of employees at our production plants reported 45,043 observations
- 4,320 barriers to safe behavior removed
KPIs
Metric |
|
2020 |
|
2021 |
|
2022 |
|
2023 |
|
2024 |
||||||
---|---|---|---|---|---|---|---|---|---|---|---|---|---|---|---|---|
Health, safety, and wellbeing |
|
|
|
|
|
|
|
|
|
|
||||||
Material topic: Health, safety, and wellbeing |
|
|
|
|
|
|
|
|
|
|
||||||
Total recordable cases1 across SIG Group |
|
– |
|
– |
|
68 |
|
65 |
|
52 |
||||||
Total recordable case rate (per 200,000 hours worked) across SIG Group |
|
– |
|
– |
|
0.86 |
|
0.80 |
|
0.63 |
||||||
Lost-time cases2 across SIG Group |
|
– |
|
– |
|
18 |
|
40 |
|
27 |
||||||
Lost-time case rate (per 200,000 hours worked) across SIG Group |
|
– |
|
– |
|
0.36 |
|
0.49 |
|
0.33 |
||||||
Total recordable cases1 in our aseptic carton business |
|
33 |
|
313 |
|
33 |
|
33 |
|
27 |
||||||
Total recordable case rate (per 200,000 hours worked) in our aseptic carton business |
|
0.83 |
|
0.60 |
|
0.62 |
|
0.60 |
|
0.50 |
||||||
Lost-time cases2 in our aseptic carton business |
|
13 |
|
17 |
|
18 |
|
21 |
|
17 |
||||||
Lost-time case rate (per 200,000 hours worked) in our aseptic carton business |
|
0.31 |
|
0.33 |
|
0.35 |
|
0.38 |
|
0.31 |
||||||
Total recordable cases1 in our bag-in-box, spouted pouch, and chilled carton businesses |
|
– |
|
– |
|
35 |
|
32 |
|
25 |
||||||
Total recordable case rate (per 200,000 hours worked) in our bag-in-box, spouted pouch, and chilled carton businesses |
|
– |
|
– |
|
1.32 |
|
1.24 |
|
0.91 |
||||||
Lost-time cases2 in our bag-in-box, spouted pouch, and chilled carton businesses |
|
– |
|
– |
|
10 |
|
19 |
|
10 |
||||||
Lost-time case rate (per 200,000 hours worked) in our bag-in-box, spouted pouch, and chilled carton businesses |
|
– |
|
– |
|
0.38 |
|
0.73 |
|
0.36 |
||||||
|
Our positive impact
Positive contribution to the United Nations Sustainable Development Goal 8.
2024 success stories
Increasing safety and productivity
Our global campaign to raise awareness of safe work behavior led to the development of a new folder-sealer by our engineering and EHS teams in Linnich (Germany). Together with local external companies, they developed a unique safety fence which not only makes the work of the operating personnel safer, but also increases the efficiency of the system.
The problem
The folder-sealer rotates at a very high speed. For this reason, safety catches and pull-in guards are installed to prevent employees from injuring their hands or fingers. These pose several challenges:
- These safety devices must be removed for repairs.
- Improper installation can lead to quality problems.
- Additional protective devices have to be designed, manufactured and installed for each new folder-sealer model, resulting in continuous follow-on costs.
The solution
The analysis of incidents and accidents in recent years led to the development of an innovative all-round safety concept designed to effectively prevent injuries and permanently increase performance. Implementation began in January 2024. The concept includes a unique safety fence that eliminates all previous finger protection devices and protective housings, while at the same time allowing employees direct and safe visual contact with belts, bearings and material flow.
The safety fence can be raised and lowered manually. As soon as the fence moves, the system stops automatically and is restarted after work on the machine. Employees are not only safer thanks to the safety-related monitoring of the fence position, but can also intervene at important points without stopping the entire machine. This means that the output of the folder-sealer is increased.
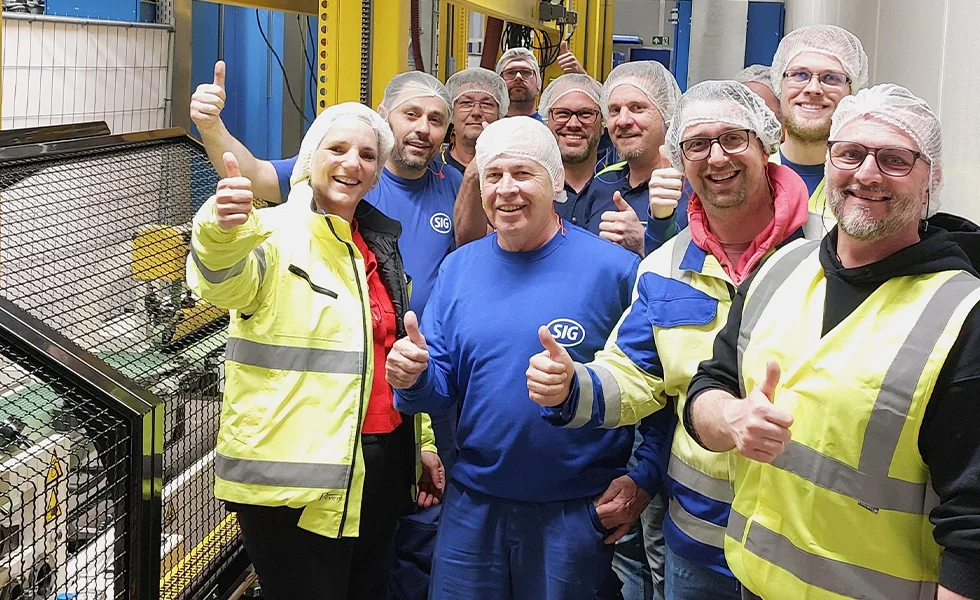
1 Based on a sickness absence rate of 2.2% (sick days per total days worked). Sickness absence and health rates are based on available data covering more than 90% of employees.
2 Severity rate based on number of days away from work x 1,000/1,000,000.
3 Industry benchmark defined as norms for manufacturing companies participating in the Willis Towers Watson employee engagement survey.